Aluminum is one of the most widely used materials in modern industries due to its lightweight nature, corrosion resistance, and versatility. However, like any material, it comes with its own set of disadvantages that must be considered when deciding its suitability for various applications. In this article, we will delve into the drawbacks of aluminum, exploring its limitations and how they impact its performance in different contexts.
From its susceptibility to certain environmental conditions to its mechanical limitations, understanding the disadvantages of aluminum is crucial for engineers, manufacturers, and consumers alike. This article aims to provide a detailed analysis of the challenges associated with aluminum use, backed by reliable data and expert insights.
By the end of this guide, you will have a clearer understanding of whether aluminum is the right choice for your specific needs, and how to mitigate its drawbacks if necessary. Let's begin by exploring the key issues surrounding aluminum disadvantages.
Read also:Tay Keith Net Worth The Untold Story Of Success And Influence
Table of Contents
- Introduction to Aluminum
- Corrosion Vulnerability
- Limited Strength
- Thermal Expansion Issues
- Higher Cost Compared to Alternatives
- Challenges in Machining
- Electrical Conductivity Limitations
- Fatigue Resistance
- Difficulties in Welding
- Environmental Impact
- Impact on Applications
- Conclusion and Recommendations
Introduction to Aluminum
Aluminum is a versatile metal that has become indispensable in modern manufacturing. It is lightweight, corrosion-resistant, and highly recyclable. However, despite its numerous advantages, aluminum has its drawbacks that can affect its performance in specific applications. Understanding these disadvantages is essential for optimizing its use.
The global aluminum market is projected to grow significantly over the next decade, driven by increasing demand in the automotive, construction, and packaging sectors. Yet, as industries continue to rely on aluminum, they must also address the challenges it poses.
In this section, we will explore the fundamental properties of aluminum, setting the stage for a deeper analysis of its limitations.
Corrosion Vulnerability
While aluminum is known for its natural corrosion resistance, it is not immune to corrosion under certain conditions. This vulnerability can lead to significant issues in specific environments.
Factors Influencing Corrosion
- Exposure to saline environments can cause pitting corrosion.
- Aluminum alloys may experience intergranular corrosion when exposed to high humidity.
- Galvanic corrosion occurs when aluminum comes into contact with other metals in the presence of an electrolyte.
Studies conducted by the Aluminum Association highlight the importance of proper alloy selection and surface treatment to mitigate corrosion risks. By understanding these factors, engineers can design systems that minimize the impact of corrosion on aluminum components.
Limited Strength
Although aluminum is lightweight, its mechanical strength is relatively lower compared to other metals such as steel. This limitation can pose challenges in applications requiring high load-bearing capacity.
Read also:How Many Points Does Experian Boost Give You A Comprehensive Guide
Strength-to-Weight Ratio
While aluminum boasts an excellent strength-to-weight ratio, its absolute strength is insufficient for heavy-duty applications. For instance, in the automotive industry, aluminum components may require reinforcement to meet safety standards.
According to research published in the Journal of Materials Science, the development of advanced aluminum alloys has improved its strength characteristics. However, these alloys often come at a higher cost, which must be considered during material selection.
Thermal Expansion Issues
Aluminum exhibits a relatively high coefficient of thermal expansion, which can lead to dimensional instability under varying temperature conditions. This characteristic can affect the performance of aluminum components in environments with extreme temperature fluctuations.
Impact on Structural Integrity
- High thermal expansion can cause warping and deformation in aluminum structures.
- Thermal cycling may lead to fatigue and failure in critical components.
Engineers must account for these thermal effects during the design phase to ensure the longevity and reliability of aluminum-based systems.
Higher Cost Compared to Alternatives
While aluminum is relatively abundant, the cost of production and processing can make it more expensive than alternative materials such as steel or plastic. This cost factor can be a significant disadvantage in cost-sensitive applications.
Economic Considerations
According to data from the International Aluminum Institute, the production of aluminum requires substantial energy inputs, contributing to its higher cost. Additionally, the recycling process, although environmentally friendly, may still involve additional expenses depending on the scale of operations.
For industries focused on reducing material costs, aluminum's price point may necessitate a cost-benefit analysis to determine its suitability.
Challenges in Machining
Machining aluminum can present unique challenges due to its softness and tendency to produce long chips. These characteristics can affect the efficiency and quality of machining operations.
Optimizing Machining Processes
- Using specialized cutting tools designed for aluminum can improve machining performance.
- Implementing chip-breaking techniques can reduce the risk of clogging and improve tool life.
Manufacturers must carefully consider these factors when selecting machining parameters for aluminum components to achieve optimal results.
Electrical Conductivity Limitations
Although aluminum is a good conductor of electricity, its conductivity is lower compared to copper, which is often used in electrical applications. This limitation can affect its performance in electrical wiring and related applications.
Applications and Alternatives
In scenarios where high electrical conductivity is required, aluminum may not be the ideal choice. However, advancements in aluminum-copper alloys have expanded its potential applications, offering a balance between cost and performance.
For industries relying on electrical conductivity, understanding the trade-offs between aluminum and copper is crucial for making informed material decisions.
Fatigue Resistance
Aluminum's fatigue resistance is generally lower than that of steel, making it less suitable for applications involving repeated cyclic loading. This limitation can impact the durability and reliability of aluminum components in dynamic environments.
Enhancing Fatigue Performance
Research published in the Materials Today journal suggests that surface treatments and advanced alloy development can improve aluminum's fatigue resistance. However, these enhancements often come at an additional cost, which must be weighed against the benefits.
Designers must consider fatigue resistance when selecting materials for applications subject to cyclic loading, ensuring that the chosen material meets the required performance criteria.
Difficulties in Welding
Welding aluminum can be challenging due to its high thermal conductivity and the formation of oxide layers during the process. These factors can affect the quality and strength of welded joints.
Best Practices for Aluminum Welding
- Preheating the material can reduce the risk of cracking during welding.
- Using inert gases to protect the weld area from oxidation is essential for achieving strong joints.
By following best practices and utilizing advanced welding techniques, manufacturers can overcome the challenges associated with aluminum welding, ensuring the integrity of the final product.
Environmental Impact
While aluminum is highly recyclable, its production process can have significant environmental implications. The energy-intensive nature of aluminum production contributes to greenhouse gas emissions, raising concerns about its sustainability.
Sustainable Practices
Industries are increasingly adopting sustainable practices to minimize the environmental impact of aluminum production. Recycling aluminum requires only 5% of the energy needed for primary production, making it an environmentally friendly option.
Companies committed to reducing their carbon footprint can explore alternative production methods and invest in renewable energy sources to support the sustainable use of aluminum.
Impact on Applications
The disadvantages of aluminum can significantly influence its suitability for various applications. From automotive manufacturing to construction, understanding these limitations is essential for optimizing material selection.
Application-Specific Considerations
- In the automotive industry, aluminum's lightweight nature is a key advantage, but its limited strength and higher cost must be carefully evaluated.
- For construction projects, aluminum's corrosion resistance is beneficial, but its thermal expansion characteristics must be managed to ensure structural stability.
By addressing these application-specific challenges, industries can harness the benefits of aluminum while minimizing its drawbacks.
Conclusion and Recommendations
In conclusion, while aluminum offers numerous advantages, its disadvantages must be carefully considered to ensure its optimal use in various applications. From corrosion vulnerability and limited strength to thermal expansion issues and higher costs, understanding these limitations is crucial for making informed material decisions.
We encourage readers to explore the resources mentioned in this article and conduct further research to deepen their understanding of aluminum's properties. Additionally, we invite you to share your thoughts and experiences in the comments section below, and explore other articles on our site for more insights into materials science and engineering.

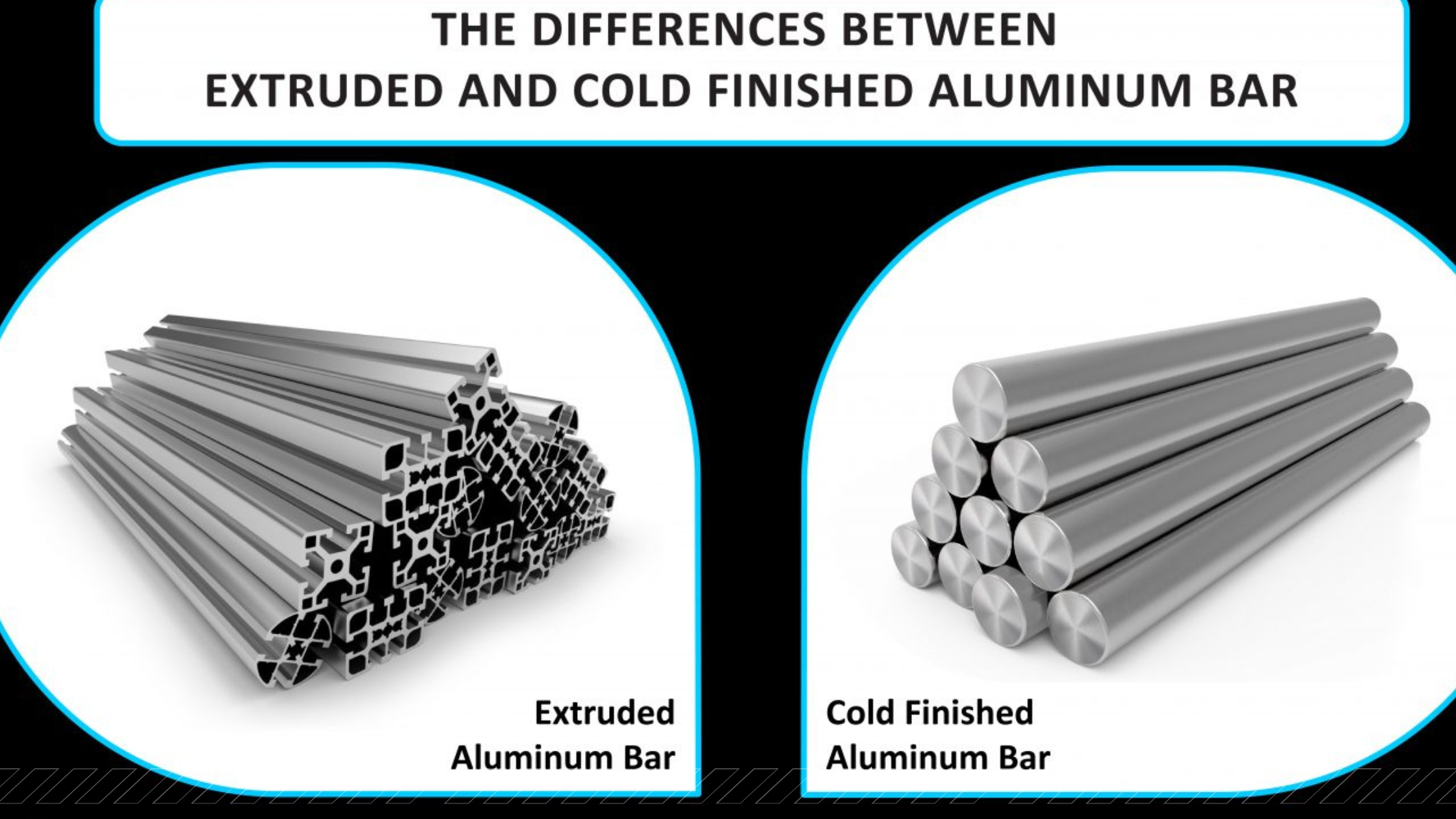
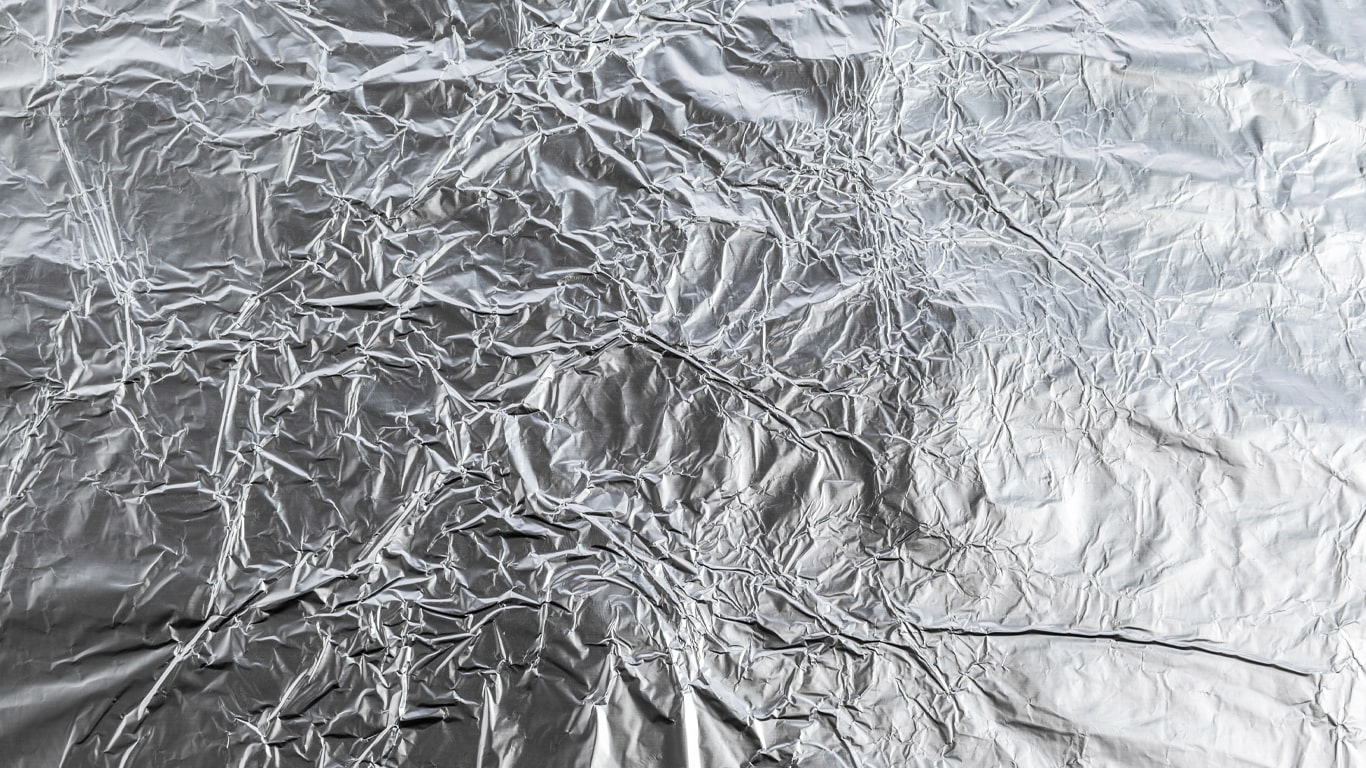